Key Takeaways
Keeping your machines in good working order is essential for any business. Regular maintenance helps to prevent breakdowns, extend the life of your equipment, and improve overall productivity.
One of the best ways to track your maintenance activity and ensure that no important tasks are missed is to use a machine maintenance history card.
What is a Machine Maintenance History Card?
A machine maintenance history card is a document that records maintenance activities performed on a particular machine and enables you to track them. It typically includes information such as the date of the maintenance, the type of maintenance performed, the parts used, and the name of the technician who performed the work.
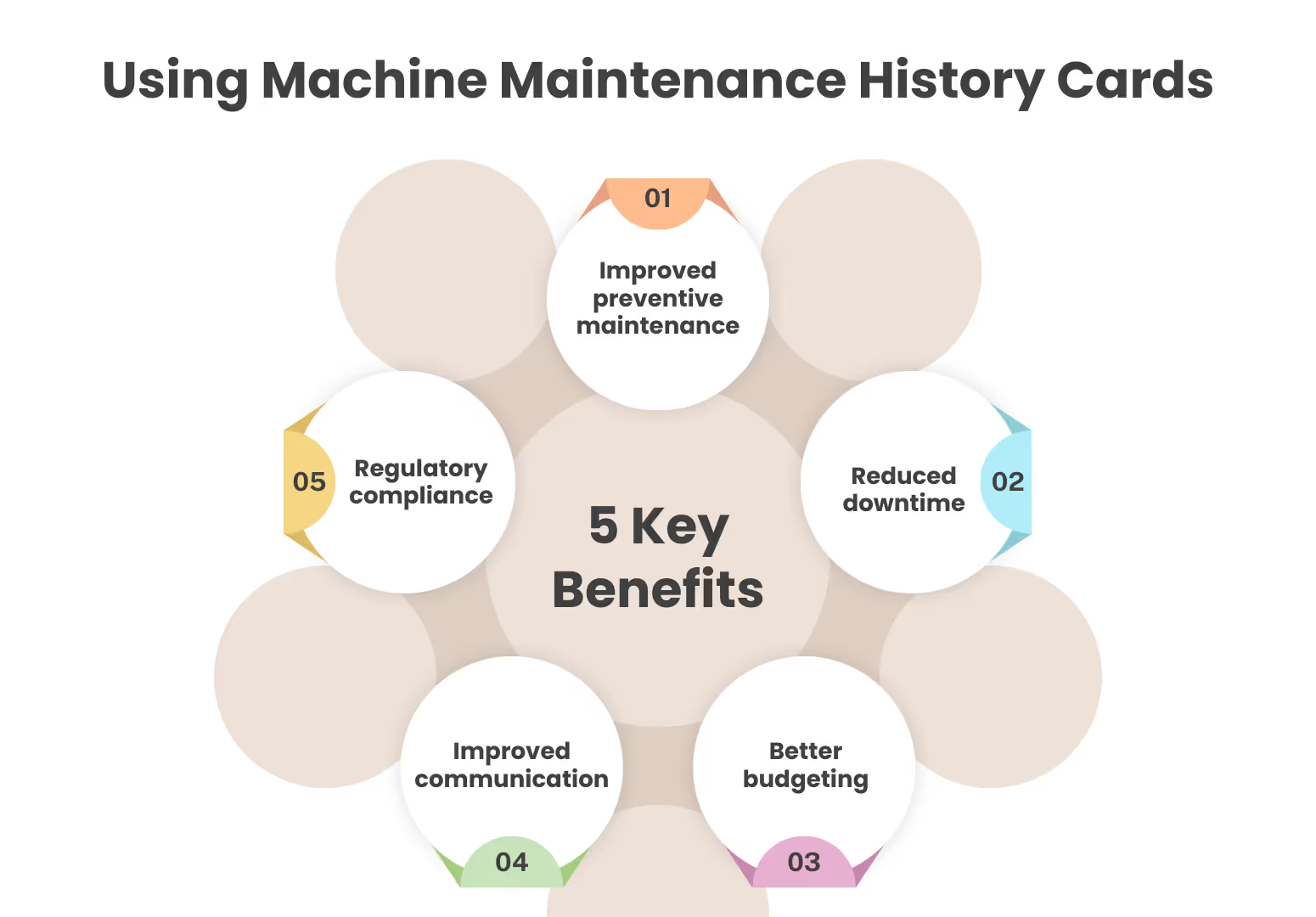
Why Use a Machine Maintenance History Card?
There are many benefits to using machine maintenance history cards. Some of the most important benefits include:
- Improved preventive maintenance: By tracking your maintenance history, you can identify patterns and trends that can help you develop a more effective preventive maintenance program. This can help to prevent breakdowns and keep your machines running smoothly.
- Reduced downtime: When a machine breaks down, it can lead to significant downtime and lost productivity. By using machine maintenance history cards, you can identify potential problems early on and take steps to prevent them from happening.
- Better budgeting: A machine history card for maintenance can help you track your maintenance costs and budget more effectively.
- Improved communication: Machine maintenance history cards can help to improve communication between maintenance technicians, operators, and managers. This can help to ensure that everyone is on the same page and that maintenance is being performed correctly.
- Regulatory compliance: In some industries, there are maintenance regulations that require businesses to track their machine overhaul activities. History card of machine can help you to comply with these regulations.
What Should Be Included in a Machine Maintenance History Card?
The specific information that is included in a machine maintenance history card will vary depending on the type of machine and the needs of your equipment business. However, some of the most common items include:
While the format of maintenance history cards can vary across organizations and the type of machinery, certain key components are universally present. A standard maintenance history card includes:
- Machine Identification: Details such as the machine's name, model, serial number, and location within the facility.
- Maintenance History: A log of all maintenance activities performed on the machine, including date, type of maintenance (preventive, corrective, overhaul), description of the task, and the name of the technician.
- Parts Replaced: Information on any equipment parts that were replaced during maintenance, including the part number, description, and the date of replacement.
- Observations and Recommendations: Notes from maintenance technicians on potential issues noticed during maintenance, along with recommendations for future action.
- Downtime Records: Documentation of any equipment downtime associated with maintenance activities, helping to measure the impact of maintenance on operational efficiency.
Download Your Free Equipment Maintenance Checklist
How to Create a Machine Maintenance History Card
There are several ways to create a machine maintenance history card. You can create a physical card, use a spreadsheet, or use a computerized maintenance management system (CMMS).
If you are creating a physical machine history card, you can use a simple index card or a pre-printed form. If you are using a spreadsheet, you can create a simple template that includes all of the necessary information. If you are using a CMMS, you can use the software to create and track your machine maintenance cards.
Sample Maintenance History Card Format
There is no one-size-fits-all format for a machine maintenance history card. The format that you use will depend on your specific needs and preferences. However, most machine maintenance history card formats will include the following information:
To better understand how a maintenance history card is structured, let's consider a simplified example:
- Machine ID: CNC Lathe - Model X1234
- Serial Number: SN00123456
- Location: Workshop A, Station 5
- Maintenance Records:
- Date: YYYY-MM-DD | Maintenance Type: Preventive | Description: Lubrication of moving parts | Technician: John Doe
- Date: YYYY-MM-DD | Maintenance Type: Corrective | Description: Replacement of spindle bearings | Parts Replaced: Bearing Model B123 | Technician: Jane Smith
- Observations: Minor wear noted on conveyor belt.
- Recommendations: Monitor belt condition for next 3 months; consider replacement if wear increases.
- Downtime: 2 hours for bearing replacement.
This format ensures that anyone reviewing the card can quickly grasp the machine's history of maintenance, understand any ongoing issues, and plan for future maintenance activities.
Tips for Using Machine Maintenance History Cards
Here are a few tips for using machine maintenance history cards:
- Keep your cards up-to-date: Make sure that your cards are updated after every maintenance activity.
- Store your cards in a safe place: Keep your cards in a safe place where they will not be lost or damaged.
- Review your cards regularly: Review your cards regularly to identify any maintenance trends or patterns that may indicate potential problems.
- Use your cards to improve your maintenance program: Use the information on your cards to improve your preventive maintenance program and reduce machine downtime.
Implementing Maintenance History Cards
Adopting tool maintenance history cards into your equipment management strategy requires a systematic approach. Here are some steps to get started:
- Standardize the Format: Develop a standardized maintenance equipment history card format that meets your organization's needs. This could be a physical card, a digital record, or part of a comprehensive maintenance management software.
- Train Your Team: Ensure that all maintenance personnel are trained on how to accurately complete the maintenance history cards. This includes understanding what details need to be recorded and the importance of timely and accurate documentation.
- Regular Review: Make it a habit to review the maintenance history cards regularly. This can help in identifying patterns, planning preventive maintenance schedules, and making informed decisions on equipment replacement or overhaul.
- Leverage Technology: Consider using maintenance management software that can digitally track and analyze maintenance data. This can provide valuable insights through data analytics, making it easier to predict future maintenance needs and optimize machine maintenance schedules.
How Digital Solutions Can Help in Maintenance Record Keeping for Equipment
Automated Data Entry:
Digital tools like machine maintenance software can connect with sensors and Internet of Things (IoT) devices to automatically record equipment data like operating hours, temperatures, and other key parameters. This automation minimizes the need for manual data entry and improves data accuracy.
Data Analytics and Predictive Maintenance:
Digital equipment maintenance logs include analytics features that analyze historical data to predict future maintenance needs. For instance, if a machine consistently requires specific repairs every few months, the system can predict these needs, enabling proactive maintenance planning.
Centralized Data Repository:
Software maintenance logs store all machine history records in one centralized location. This makes it easier for teams to access asset repair history, analyze trends, and make informed decisions. Centralization is especially useful during audits or inspections, where quick access to complete records is crucial.
Related Posts
- 9 Steps to Create an Effective Equipment Maintenance Log in 2024 (With FREE Template)
- Heavy Equipment Fleet Maintenance Software
- Deciding When to Repair Vs. Replace Heavy Equipment
Final Words
Maintenance history cards are an important element in the maintenance of machines and equipment management framework, offering a detailed and organized method to track maintenance activities. They not only facilitate preventive maintenance planning but also contribute to operational efficiency, compliance, and cost management.
Elevate your fleet's efficiency with Simply Fleet! Streamline maintenance, reduce costs, and optimize operations. Start your journey toward seamless fleet management today.